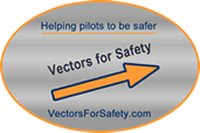
- Home
- Articles
- Privacy Policy
- Home
- Articles
- Privacy Policy
Safety After Maintenance
Continued from Vectors for Safety - December 2022
This pilot reported a scary event five minutes after departure on an initial flight after maintenance that resulted in declaring an emergency and returning to the departure airport.
I owned a 1974 A36 Machen turbo conversion. AP had always told me the space inside the cowling is very tight and a pain to work on. I do not know if that led to the problem but here’s my story.
Had my magnetos worked on and on the maiden voyage took off on an IFR flight when 5 minutes into my departure my alternator out light illuminated. I told my wife we’d have to turn around and get it checked out. We were in clear air and I had terrain avoidance visually which was relayed to departure control. As I started my 180 degree turn back smoke began filling the cabin from every orifice capable. I quickly had no outside vision. I opened both my little windows (I had one on each side) but the smoke influx was greater than the smoke efflux and it just got worse. Also, it was acrid like electric fire so I was pretty terrified. I notified departure control and he asked if I wanted to declare an emergency and I stated it would be a great idea. Souls on board and fuel remaining freaked my wife out more than the smoke in the cabin. She always loves the backseat to herself and our dog so she didn’t get the brunt of the smoke. Anyway, I quickly dialed in the opposite runway ILS and flew the instrument approach with little to no visibility. Finally at about 1000 AGL the smoke stopped coming and the efflux was sufficient so I could see to land. I almost forgot to GUMP but I always call out “3-green” when I see the runway…I was lucky I had the electrical power to put gear down but I went 3-green on a mile final. Tower had emergency vehicles at each of the taxi turnoffs and had halted all traffic on the ground and inbound. I made an uneventful landing and taxied to my FBO with fire trucks in front and behind me.
Upon a week’s worth of review, it was decided one of the exhaust manifold bolts was not torqued to the correct tightness and 1400 degree EGT came out and fried a huge (probably 1.5 inch diameter) wire bundle into a black molten charred mess. All things electric in that bundle failed and my alternator was effectively detached from the panel. How my nav, com and gear survived I guess they were just in another bundle.
This pilot reports multiple issues that could have had unhappy endings but were resolved safely.
When I was flying, fortunately only about 10 nm from a “major” airport, a pushrod broke. I had sufficient power to land safely at the airport. Anyway, the partnership decided to ship the engine out for a major teardown and inspection. We entrusted our local mechanic with the removal and installation of the engine. He said he could do a top overhaul. I am forever grateful that we declined that work!
When we got the plane back, and had flown it home, we found that the mechanic had left his safety wire pliers in the engine compartment. A few flights later, we discovered that a hose had not been properly tightened.
Fast forward to the oil change after break in. Upon landing after the oil change, there was lots of oil on the wing strut and belly of the plane. The mechanic had not replaced the safety wire on the drain plug on the oil cooler. It had backed out about 1/4 turn.
Fast forward again to the first night flight. The landing light was not working; a ground lead to the light was not tight. Was that a failure to tighten it properly? Or had it simply worked loose? We don’t know.
All of these things had good endings but could have ended up very differently. (Well, except the landing light. Given a good pre-flight, that would likely not have been an issue in flight.)
Our mechanic admitted to being overworked. He has hired an assistant. I think the safety wire incident scared him a bit. We have not fired him, but we are very cautious. His other work for us has been OK.
As an aside, when the engine was torn down, the engine shop found an old bird carcass. It was not visible until the engine was torn down. Our current best guess is that it had interfered with the engine cooling and caused first, a sticking valve (thought to be a deposit that we thought was fixed), and next, the pushrod failure. The engine was otherwise undamaged; our wallets escaped worse trauma!
This pilot tells of dangerous condition caused by a rag left in an air inlet after an oil change. He also relates recommendations.
As a member of a local club, I planned to fly a club Cessna 172N from Oklahoma City to Chicago with my teenage son as a passenger. We were above a 3 or 4000 foot thick overcast, over NE Oklahoma, when we smelled something burning. When I got a faint wisp of smoke from under the panel, I declared an emergency, shut off everything electrical that I didn't need to fly an approach, and got vectors to the nearest, and flew an approach without incident (a testament to good training that I kept the needles from pegging while puckered up from fear).
After landing, we found no evidence of fire in the panel wiring or in the engine compartment. The next day, being clear and a million, and still thinking I had an electrical problem, I decided to do a runup and if I found no issues, I would take off and fly home with a backup plan to shut off the master and land if I found smoke or whatever. (I had driven my son home via the airport car so I was only exposing myself to the danger, just in case you're wondering what kind of dad I am;-)
During the runup, I got lots of smoke from the cockpit air vents. I shut down the engine, grabbed the fire extinguisher, and ran to the cowling to find visible flames coming from the heater inlet opening. After putting out the fire, I pulled an oily rag from the opening (which proceeded to spontaneously burn again). Turns out I was the first to fly the airplane after the maintenance shop had changed the oil.
The rag was shoved into the opening far enough that it was touching the heater muff.
In hindsight, I could have seen that rag if I had really tried to look into the opening. It never occurred to me to do so. Since then, I've adopted a philosophy I've heard others promote, which is if you can see it without disassembling the airplane, even with a mirror, then you should look during preflight.
Also, since then, I've bought my own airplane(s), and one of my partners is an A&P / IA. From him (and my experience above) I've also learned not to take ANY maintenance, no matter how "minor", for granted. There's always a potential to make something worse while fixing something else, even something as simple as changing the oil. Do a more thorough preflight, an extended runup, and consider a high-power climb near the airport, or a few trips around the pattern, after any maintenance (and before piling in the passengers).
Doing owner-assisted annuals is this pilot's answer to maintenance problems he has encountered.
1- upon test flight cabin filled with smoke. Returned to base and found rag that fell into air intake for heater.
2-upon test flight avgas poured onto my leg from fuel pressure tubing due to maintenance disturbing the fuel line during annual inspection.
3-Maintenance was jacking up Cessna 210 and didn't understand that you don't use additional support as Jack's will slide off if the primary Jacks are changed from wings to fuselage which ended up the jack sliding off and puncturing the tank. So now I do annuals myself [ owner assisted].
This was not an error by maintenance but could have ended badly. This pilot recounts an event that prompted a checklist modification.
I took my Aztec up for its first flight after annual one year. The runup seemed normal so we took off. Shortly after takeoff, the plane began yawing hard to the right. It felt just like losing an engine. Fortunately, I had a second pilot along so I continued flying while he did troubleshooting.
It turned out that someone had run the rudder trim control all the way to the stop while doing the annual and never put it back. I followed my checklist which says "trim for takeoff" but it doesn't specifically mention rudder trim, a control I almost never touch.
It all turned out well but it might not have. If I had quickly shut down what I thought was a bad engine, I'd now be low, slow, and climbing on one engine. And worse, if I'd had an actual engine failure, the added yaw might not have been correctable with rudder input alone. That could have been really bad.
Despite knowing to be extra careful with the preflight, I still missed that item. So did my co-pilot. Still, I was really glad I had him along for the flight. And I've now made an extra entry on the checklist under trim. I added the word "both".Finally, Greg Wobster, provided some valuable insight as a designer of industrial equipment. Greg writes:
Cleaner is Better: It's far easier to spot something leaking when the equipment is spotless. This is especially true with fresh oil or other clean liquids. That goes for the area underneath. If you're in a Hanger, craft paper on the floor will even be an aid in showing where drips had occurred and evaporated.
Brighter is Better: The brighter the light, the more detail you'll be able to see.
The time it takes to remove a guard/cowling/access panel is insignificant compared to the time for a repair from not removing it. If possible, take a good look after an initial run before anything is closed-up.
Over the years of designing equipment, I've learned that no matter how many times (or people) check something, something will eventually get missed. A layered approach of duration and detail of inspection provides for the best opportunity to find errors and omissions while minimizing the risk.
Not all maintenance errors end well for the pilot. This pilot lost engine oil pressure on the return flight home after an annual inspection on his CTLS. The engine seized and the pilot could not reach an airport so he pulled the chute. Fortunately, he escaped with minor injuries, but the airplane was likely damaged beyond repair. Though the final NTSB report has not yet been issued, two engine oil hoses were found disconnected. This accident is one of our featured accidents in the December 2022 issue of Vectors for Safety.
Copyright © 2025 Gene Benson. All rights reserved.